Innovation Track – Wanderful.Stream
➤ Le challenge de JD’C Innovation
Au départ de chaque projet Wanderful.stream, il y a 2 éléments-clés : l’existence de déchets inexploités et une volonté de les retravailler. Suffisent-ils pour construire un projet d’économie circulaire ? Non, comme en témoigne l’expérience de JDC Innovation qui a pu mettre en évidence, dès les premières étapes de son projet d’orthèse médicale, une problématique liée aux coûts de mise en œuvre. Accompagnée par EKLO et Philippe Swimberghe, designer industriel, l’entreprise a donc remis en question son concept initial : de nouvelles solutions sont déjà à l’étude pour valoriser les qualités techniques de la fibre de carbone !
Itérer pour explorer tout le potentiel d’un matériau à haute valeur ajoutée
Rencontre avec Simon Augustin, Responsable de Production chez JD’C Innovation
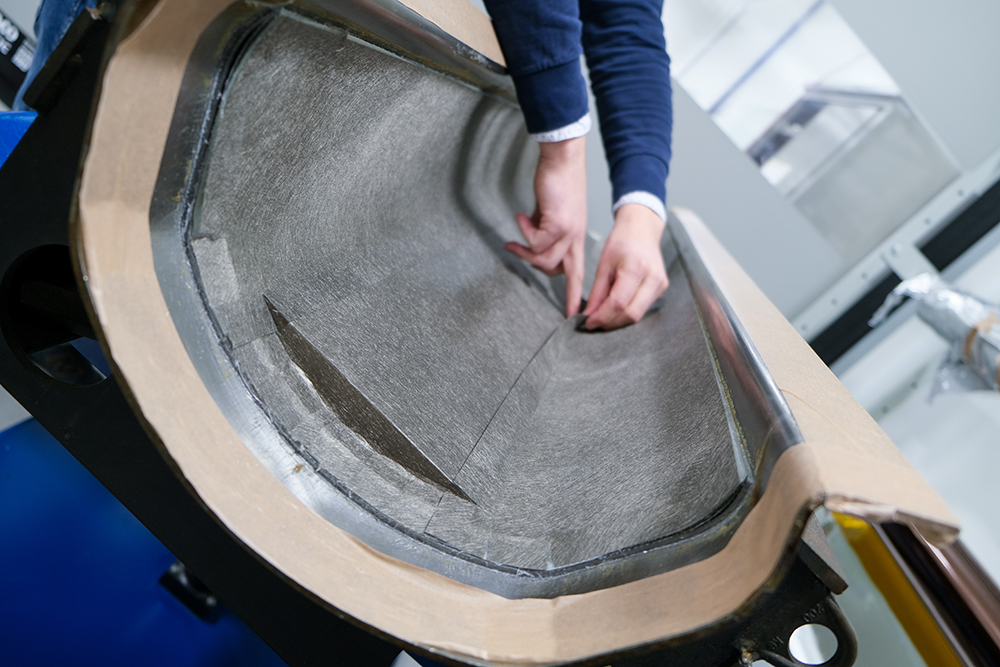
JD’C Innovation est une PME à finalité sociale active dans la conception et la fabrication de pièces en matériaux composites pour les secteurs de l’aéronautique, de la défense et de l’automobile. La structuration de pièces autoclavées en bâches sous-vide génère des déchets de polyéthylène, de fibre de carbone et de fibre de verre, issus de la découpe des matières premières.
C’est dans une logique de certification environnementale, alliée à une demande croissante des clients, ainsi qu’une volonté de diversification de ses activités qui ont provoqué dans le chef de l’entreprise une réflexion sur la manière de retravailler et valoriser ces déchets de haute valeur dans un projet propre.
Le travail initial mené avec les étudiants lors du bootcamp Wanderful.stream avait débouché sur un projet d’orthèse médicale qui, bien que séduisant pour JD’C du point de vue de la pénétration du marché, a très vite montré ses limites en phase de recherche et d’analyse…
« Comparé au prix d’une orthèse classique sur le marché, les excellentes qualités techniques du carbone ne justifient pas le prix élevé qui aurait dû être pratiqué pour couvrir les frais de production de la solution médicale »
Simon Augustin Responsable de Production chez JD’C Innovation
Très vite, accompagnée par EKLO et Phillipe Swimberghe, le designer en charge du projet, l’entreprise a remis en question sa solution et part à présent sur d’autres options actuellement à l’étude.
« Une nouvelle étude du marché devra nous orienter car ces options posent de nouvelles questions : certifications, assemblages techniques, sécurité, standardisation…etc. Autant d’inconnues qui devront faire l’objet d’une validation de la faisabilité de la solution par rapport au marché. Chez JD’C, on se réjouit déjà de voir la suite ! »
Simon Augustin Responsable de Production chez JD’C Innovation
Le vrai challenge du designer ? Partir d’un déchet et non d’un besoin !
Rencontre avec Philippe Swimberghe, Designer industriel – Phil Design Studio
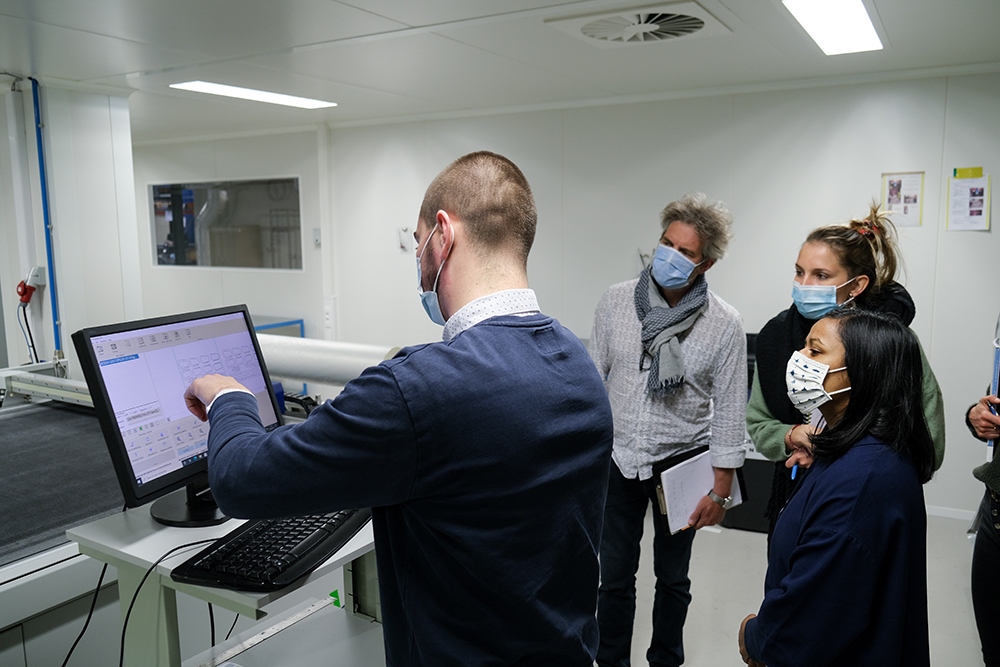
Accompagner JD’C Innovation pour exploiter la matière issue du puzzle de pièces de carbone produit par JDC Innovation, tel est le défi qu’a accepté Philippe Swimberghe, Designer industriel et fondateur de Phil Design Studio.
Très vite, dans le projet d’orthèse médicale initialement porté par l’entreprise, le designer a pu observer le risque lié à une fabrication peu rentable car disproportionnée par rapport au prix de vente du marché. Mais ce n’était pas la seule contrainte.
« L’inadéquation entre le coût et le prix de revient s’ajoute à des questions d’ergonomie, de fabrication sur-mesure, de faible durée de vie du produit et, si l’on va encore plus loin, de risque d’absence d’intervention des mutuelles pour un produit jugé trop onéreux. L’intérêt technique de la fibre de carbone n’en fait pas pour autant un matériau simple à exploiter »
Philippe Swimberghe, designer industriel – Phil Design Studio
Toutes les parties s’impliquent à présent dans la recherche d’une nouvelle solution. Ce qui prime, pour le designer, c’est la recherche de réalisme et l’adéquation avec la volonté de l’entreprise : recherche-t-elle la différenciation, la valeur-ajoutée, une production de grande quantité, la simplicité de production, l’adaptabilité de la solution proposée ou sa simplicité ? Ou tout cela à la fois ? Ces questions sont autant de challenges auxquels Philippe tente de répondre en faisant appel à ses méthodes de designers, dans un cas d’école qui est cependant sensiblement différent des demandes habituelles.
« Ici, on ne dessine pas l’objet d’abord, au départ d’une demande ou d’un besoin : on part de la matière dont on dispose et c’est en fonction d’elle que l’on travaille un produit. La remise en question du projet nous pousse à repartir du cahier de charges en se posant la question « simple » suivante : que pourrait-on construire de très petit en utilisant la fibre de carbone ? C’est ainsi que nous remettrons le processus de réflexion dans son ordre logique ! »
Philippe Swimberghe, designer industriel – Phil Design Studio
Article co-rédigé par Emilie Parthoens et Julie Toby
avec le soutien du Fonds européen de développement régional.
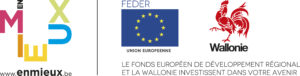